ESREF 2020—Best Paper Award
The Best Paper Award Committee (BPA) of the 31st European Symposium on Reliability of Electron Devices, Failure Physics, and Analysis, ESREF 2020, have chosen CSEM’s Maxime Auchlin’s and co-authors’ paper entitled “Can automotive MEMS be reliably used in space applications? An assessment method under sequential bi-parameter testing” to be presented at the International Symposium for Testing and Failure Analysis (ISTFA) 2021, in the USA.
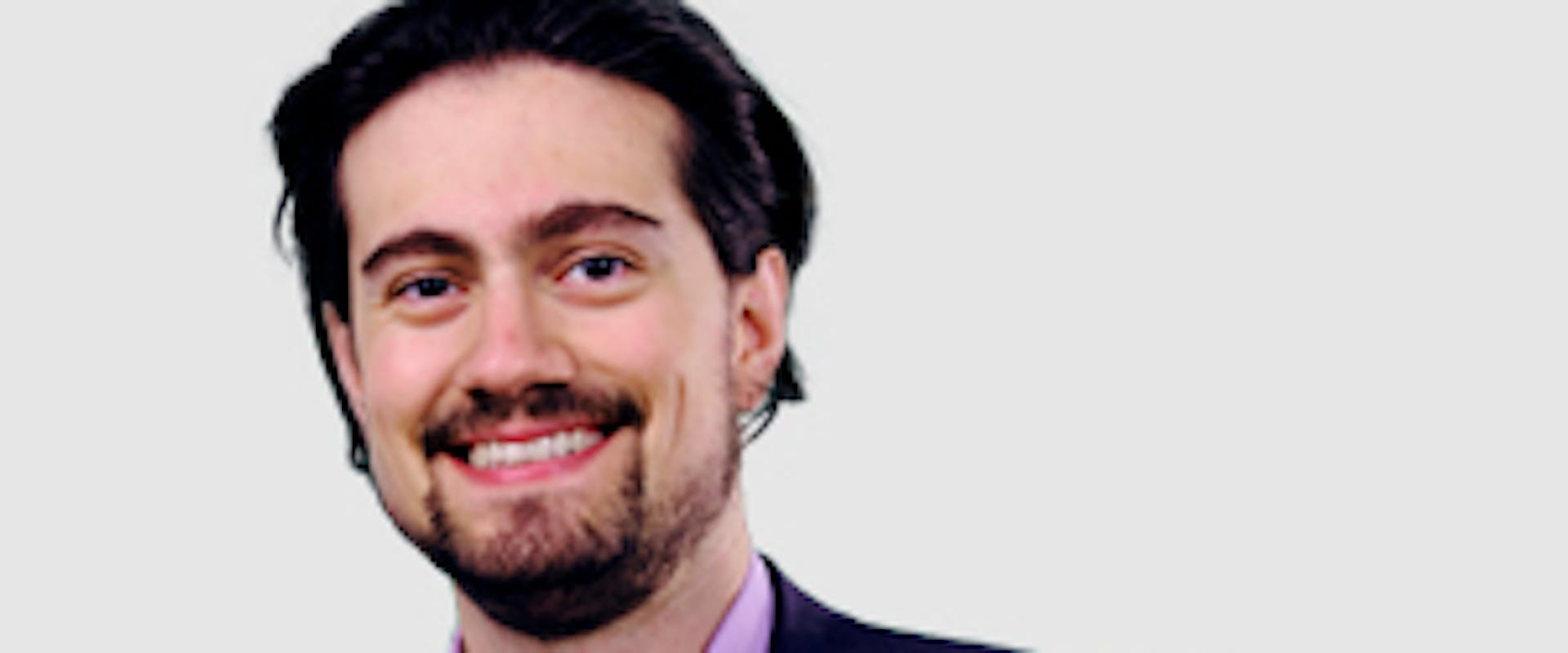
Driven by CSEM, with the backing of the European Space Agency Networking/Partnering Initiative and EPFL Swiss Space Center, the study is based on the results of Maxime’s Ph.D. thesis, which he wrote while in the Materials Science and Component Reliability group at CSEM.
The award-winning paper reviews if commercial sensor devices found in the automotive industry can be applied to space applications. IMU or Inertial Measurement Unit devices are typically found in car electronic stability program (ESP) systems and measure motion alongside other parameters using a combination of integrated accelerometers/gyroscopes.
While these super robust automotive devices pass traditional reliability assessment methods without a problem, they can fail when subjected to multiple parameters on a cumulative scale. For example, during the study, a set of IMU devices were subjected to a thermal cycling campaign then was sent for vibration testing, which resulted in its destruction. Conducted separately these tests don’t lead to the device’s failure but when subjected to the stress of cumulative testing it metaphorically ‘cracked under pressure’.
More traditional MEMS device reliability assessment and qualification test flows used by space agencies are incapable of yielding conclusive results that enable the proper definition of a device’s actual degradation and lifetime. Regardless of the currently applied procedures, failures of devices are still occurring in-orbit, despite ground testing recording no noticeable failures from these robust components. The novel method proposed by Maxime & his co-authors in their paper aims to solve this issue and bring confidence to the concept that sensors from the automotive field can be used in space applications so long as they are not subjected to testing under certain test patterns, which are described below.
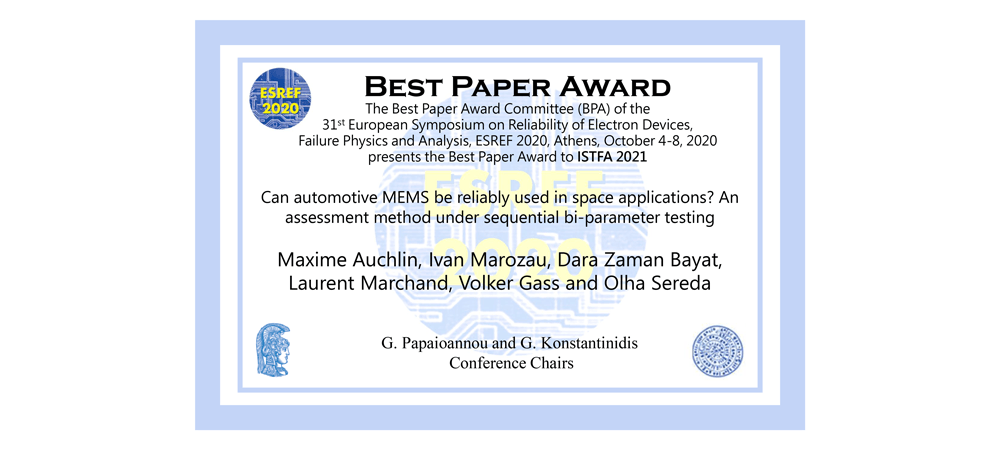
Results in brief
Commercial-off-the-Shelf (COTS) automotive inertial measurement units were subjected to severe accumulative stress conditions: thermal shocks (high-temperature gradients), temperature cycling (low gradients), and vibration. These stress conditions are combined in an A-then-B sequential testing procedure, with the aim to promote failure acceleration and improve lifetime prediction. The maximum stresses, applied individually, did not cause failure on the selected components. However, accumulative bi-parameter testing conditions resulted in die attach delamination.
Three batches of devices tested with different preconditioning (A-then-B or B-then-A) display different reliability figures. Failure was only observed in the sequence: temperature cycles followed by vibration. The conditions of testing were significantly harsher than the usual operational conditions for the devices. Failure mode and effects analysis (FMEA) was established. A Finite Element Analysis (FEA) is then also undertaken based on a destructive physical analysis of the devices to confirm the correlation between the stresses applied and the physics of the failure, to understand the thermomechanical behavior of the devices and link it to observed failures.
Overall, the automotive devices demonstrated very high robustness to the selected conditions of testing, themselves being already harsher due to their definitions rooting in the military field via the standards used in the space field. While further and more various testing remains essential to fully qualify for a space mission, it can confidently and safely be shown that these devices can be used for space application on the thermal and vibration aspects.