June 29, 2021
Predictive maintenance for wind turbines
Failure of components within wind turbines is a costly exercise, but thanks to Artificial Intelligence (AI), breakdowns are becoming a thing of the past. Together, data scientists at Proxima Solutions and CSEM have developed a series of AI algorithms that offer early detection of anomalies in wind turbine behaviors, allowing quick corrective maintenance measures to be taken to prevent machinery breakdowns. The algorithms were tested at BKW wind farms across Europe with great success and are integrated in commercial solutions.
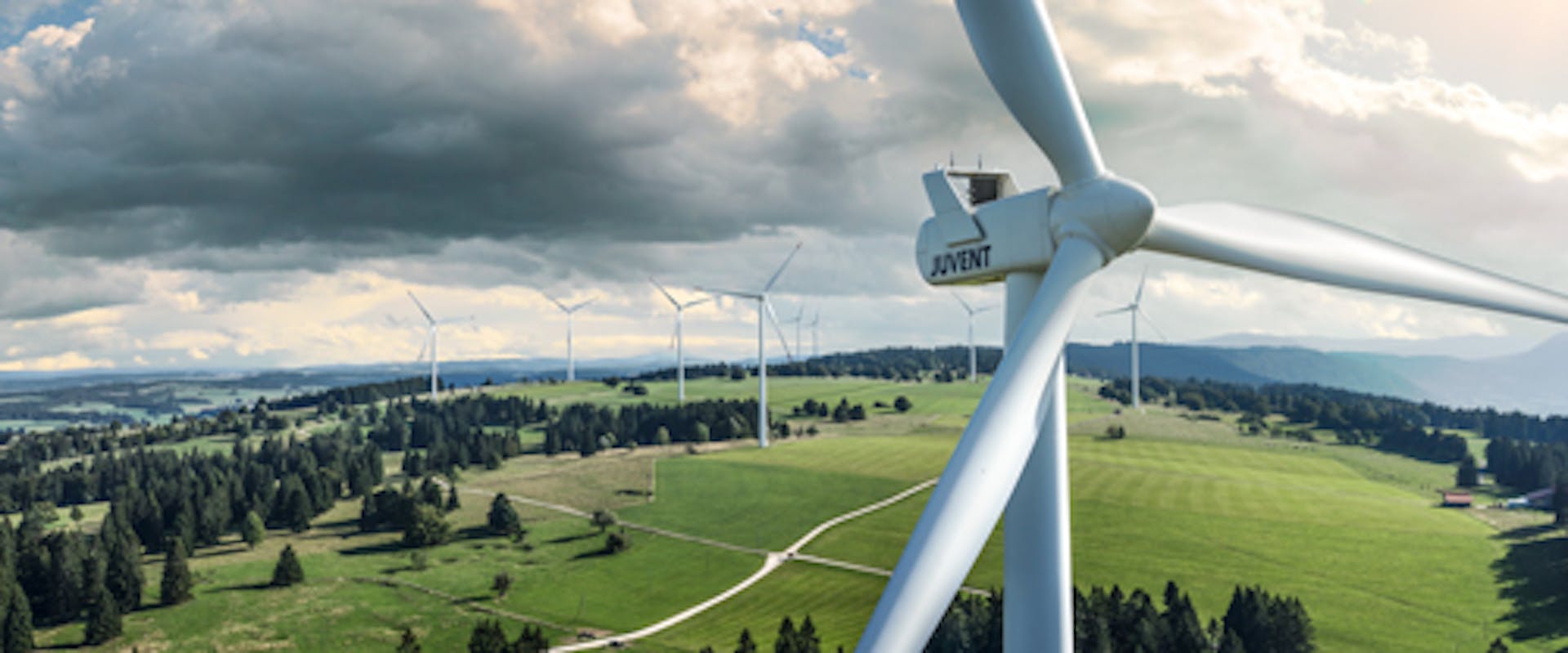