February 3, 2023
Making personalized cancer therapies accessible to all
CSEM has supported Lausanne-based start-up Limula in its mission to make cell therapies more affordable, and to facilitate access to these personalized treatments. The start-up's technology enables the automated production of CAR T and other cell therapies at scale. With CSEM's help, Limula has moved its technology beyond prototyping towards pre-industrial stage.
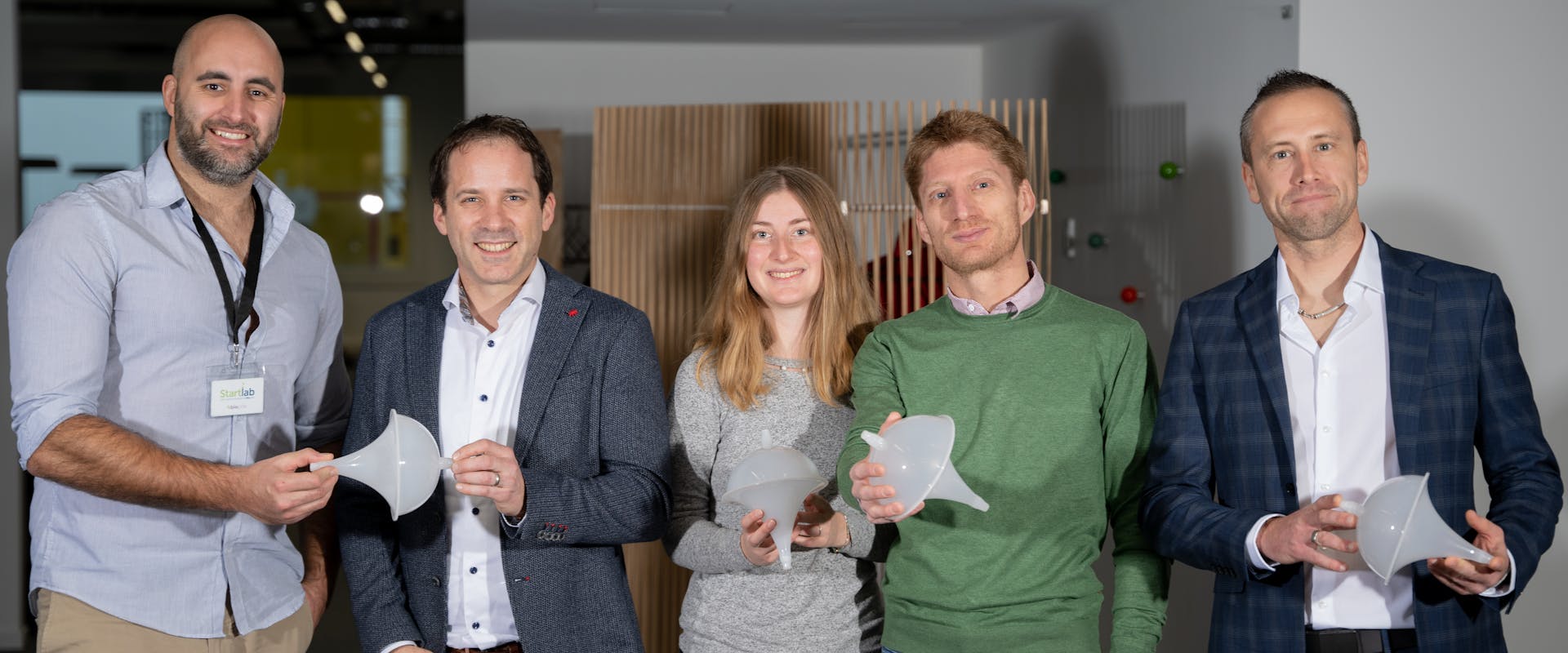
© CSEM - Successful collaboration between start-up Limula and the Swiss technology innovation center CSEM: Yann Pierson (Limula, CTO), Vincent Revol (CSEM, Co-Head Research & Business Development Life Science Technologies at CSEM), Diane Ledroit (CSEM, Senior Engineer Cell Microtechnologies), Luc Henry (Limula), and Gilles Weder (CSEM, Co-Head Research & Business Development Life Science Technologies at CSEM). They hold a disposable Limula Kit in their hands (from left to right).